Fabtech Expo Report: MDPH2 printing on an IRB 4400!
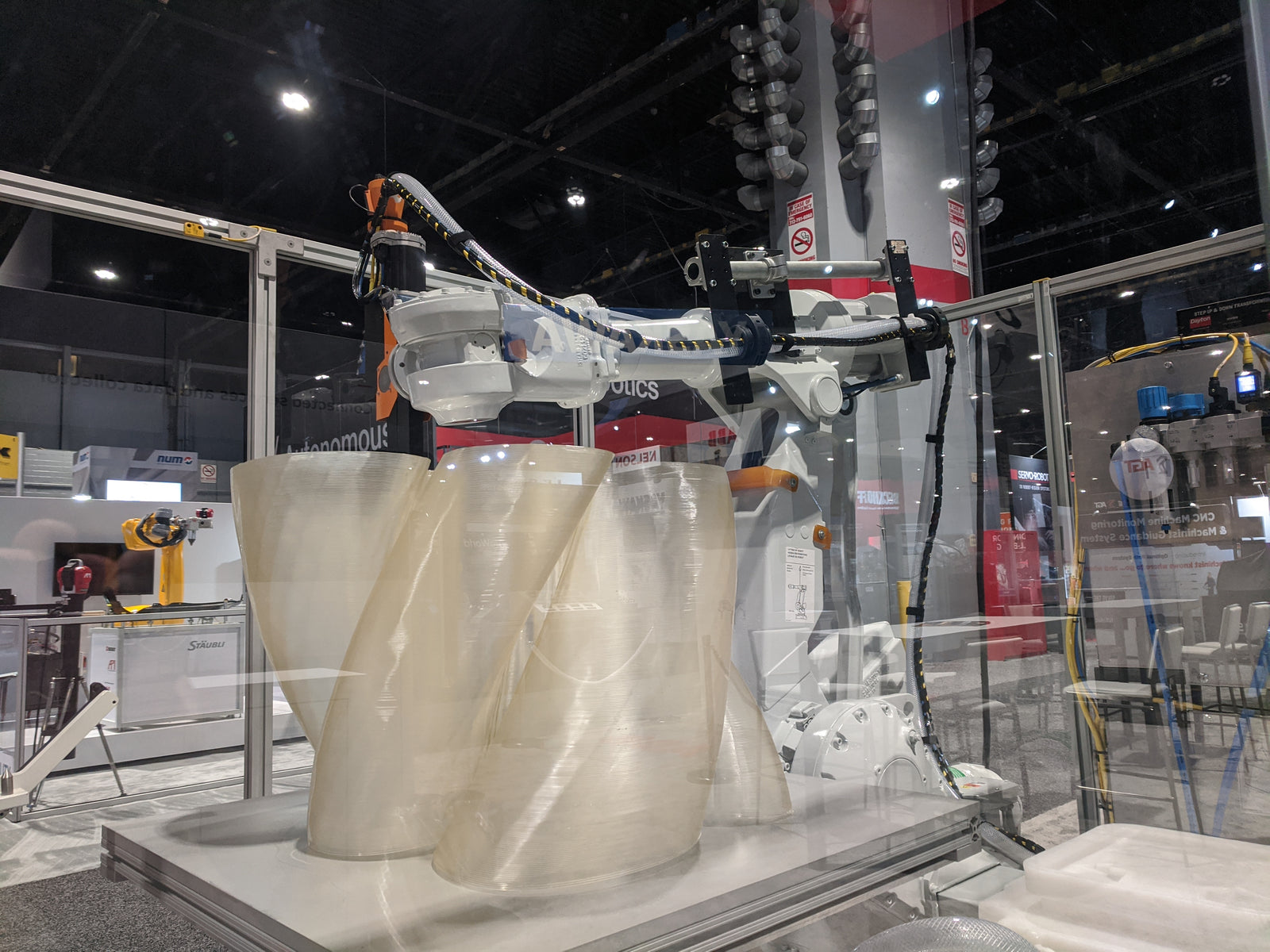
The Massive Dimension team is back from our trip to Fabtech 2021, the biggest fabrication convention of the year, held in Chicago. We had a blast, made all sorts of new friends, were inspired by technological innovations, and showed off our own hardware as well! It was an incredible event and one that we are glad to have attended. There was an entire additional conference running concurrently in a separate section of the convention center called RAPID which was focused on additive manufacturing which was also full of marvels. We saw a 3D printer geared towards making microscopic prints with a resolution of 0.4 microns, and on the opposite end of the spectrum, we saw a gigantic printer with a ½” nozzle and a roller that swiveled to stay behind the extrusion and flatten it to its finish width. The dominant fascinations at RAPID seemed to be metal printing (hard stuff) and elastomeric materials (squishy stuff). While there was much to see at RAPID, our main focus was on Fabtech and our collaborative demonstration with ABB.
Unless we missed one amidst the hundreds of booths and demonstrations, we believe the ABB/Massive Dimension printing cell may have been the only instance at the conference of an extruder mounted on an industrial robot. Our MDPH2 was integrated on an IRB 4400, which had an additional seventh axis of motion granted by attaching the heated print bed to a rotary positioner. The rotation of the bed in concert with the motion of the arm was quite hypnotizing to watch, and you can imagine how a larger bed could be implemented to enable a smaller arm to achieve print sizes beyond its conventionally defined reach. ABB has another variation of this positioner which can tilt through an additional axis, which we would love to someday see in tandem with a print head, as it would enable non-traditional print geometries to be realized.
The IRB 4400 is capable of carrying a 60 kg payload, which means that it could actually carry two of our MDPE10 extruders! A few people at the demonstration asked why we used such a large robot in a relatively small cell- the particular robot was chosen not so much for its size and reach as for its accuracy and repeatability. We chose to display this by running a single-walled print (3 mm line width) with overhanging geometry that would be revealing of inaccuracies in the deposition- but there were none. The layers were beautiful and you could see the polygon faces from the original model after being scaled up so enormously. At first, we remade the model to smooth the polygons, but a team vote decided to revert to the “patterned” version as having more visual interest.
It was a rewarding experience to be able to work so closely with the process engineers at ABB on this project. They brought to the table all of the necessary know-how to integrate the extruder and its accessories into their motion controls, including everything on the software side to take a conventionally sliced g-code and convert it into a protocol for the robot. One of the goals of the demonstration was to showcase their recently developed 3D Printing Powerpac plugin for RobotStudio, which has the capability to do just that- we sliced the .stl in Cura then imported it into RobotStudio and were able to run a simulation of the print and export the converted machine instructions to the printing cell. We were able to offer our experience with 3D printing and our extruder to help fine-tune the extrusion settings and provide some helpful tips on the slicing settings- as many of the process engineers came from different backgrounds such as welding. To see the sum of these different knowledge bases come together and in a very short time be manifested in a functioning printing cell was an immensely satisfying experience- and we had a lot of fun along the way!
We are very excited to keep working on this collaboration with ABB and hope to see more of our extruders (including, of course, the MDPE10!) mounted on their industrial robots in the months to come. We are only just scratching the surface of what is possible with these combined technologies and moving forward see huge potential for advancing large-format 3D printing and expanding possibilities into the realm of non-traditional, nonplanar geometries! We’ll be sure to keep you updated on developments in this new frontier, so stay tuned!
Below are some photos and video from the Fabtech Expo:
1 - MDPH2 ABB Demonstration at Fabtech
2 - The printing cell including hopper for automated feeding and control boxes
3 - Heated bed on a rotary positioner
4 - A crowd drawn in by hypnosis
5 - The aptly named "Twisty Spiral"
6 - Experimenting with colorant
7 - Some of the dorks who made it happen
8 - Initial layers test
9 - A long reach